The WRL 8012 cross-wedge rolling line (with one movable flat tool) is designed to produce forgings of the type of bodies of revolution with a diameter of 35-80 mm and a length of up to 420 mm by hot rolling. It is used in the production of a large range of parts, mainly for subsequent stamping or mechanical processing in the production of suspension parts and gearbox shafts for trucks and automotive equipment.
• Rolling mill capacity - 120 kW (working mode is 35-40% less);
• Length of the forming part of the tool - 1250 mm;
• Time for changing tools - 30 minutes (the line uses bolted fixation of the replaceable tool) or 15 minutes (hydraulic automatic tool clamping);
• The control system based on PLC (Mitsubishi) consists of a control panel and an electrical cabinet (upon request, it is possible to use controllers from other manufacturers - Siemens, Omron, Allen Bradley). Design of control systems in accordance with the region of operation (CIS, USA, etc.)
• Adjustment of the closed height using the remote control during operation;
• Rolling is carried out from individual blanks - the heated blank is fed into the machine from the side by the machine loading mechanism. The machine, using the tool, rolls - forms the forging. After rolling, the finished forgings are removed along the tray into the container.
• The upper slider drive is hydraulic. The machine is equipped with a system for maintaining a constant thermostatic rolling mode (tool cooling).
• The control system, based on a programmable controller, allows the line to operate in setup and automatic modes with all settings displayed on the operator panel;
• Operator diagnostics and assistance system (internal continuous diagnostics);
• High degree of automation. Ensures uninterrupted and stable operation of the line with full control of all parameters (including in combination with an induction heater, control of the heating temperature of the blanks and rejection or feeding of the line, a system for cyclic feeding of blanks from a slide hopper, rolling of forgings and transfer to the next stage);
Includes an induction heating unit with a thyristor frequency converter with a capacity of 800 kW 1000 Hz and 2 sets of replaceable inductors. Automatic feeding of blanks into the inductor from the storage tray. The loading mechanism drive is hydraulic. When replacing one inductor size with another, quick readjustment is provided (connection of water-cooled pipes with quick-release nipples, fastening of the inductor with quick-release latches). The inductor design (lining) is disassemblable and repairable with the help of ceramic insulators. Water-cooled guides are provided for moving blanks along the inductor.
The installed capacity of the entire equipment complex (rolling machine + heater) is 920 kW. The equipment uses an original dual-circuit cooling system for the main working units of the tool, rolling machine, hydraulic stations, inductors and TFC. Cooling of heated units and elements of the line is forced water with continuous water supply at a pressure of 0.25...0.4 MPa. Cooling of the TPC is dual-circuit with a heat exchanger. The primary closed circuit with a heat exchanger is connected to the cooling system of the TPC cabinet, the secondary circuit is connected to the process water supply system. The coolant of the primary TPC cooling circuit is distilled water.
When rolling forgings with a flat tool on the WRL8012 line, we have the following advantages:
• higher accuracy of the resulting forgings
• high productivity
• easy tool change due to fixing the rolling tool on the WRL8012 line with bolts
• tool installation does not require additional basing and parallelism.
• the tool has a cooling system to stabilize the temperature mode of the line in automatic mode.
• flat tool of WRL and WRL TS mills is easier to manufacture and maintain during regrinding (only part of the replaceable wedges requires repair, while the entire surface of the roll (roller) is regrinded when regrinding a round tool).
• automatic adjustment of the closed height from the control panel of the rolling line for switching from one diameter of rolled blanks to another.
• equipment for 2-3 shift operation.
• compact arrangement of equipment during transportation and logistics (experience in delivery by road, rail, sea and air transport)
Cross-wedge rolling line WRL8012
Rolling machine, sorting mechanism, machine loading device, induction heater, inductor loading device, central control panel
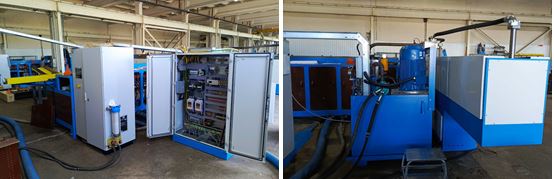
Thyristor frequency converter of induction heater / Control cabinet with open doors / Hydroelectric power station
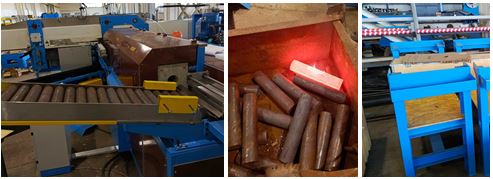
Set of replaceable inductor No. 2 (mounted in the induction heater) with automatic feed device from the storage tray. Assembly table for servicing rolling tools
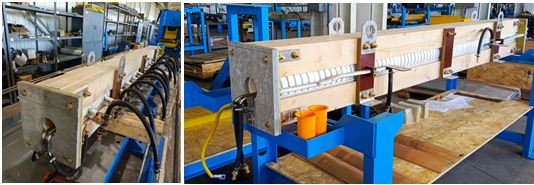
Replacement inductor kits
Planning solution for the WRL8012 line
Placement of part of the line during transportation of a Eurotruck 1
Placement of part of the line during transportation of Eurotruck 2
WRL8012 cross wedge rolling lines are used for rolling forgings for stamping or metalworking (ball pins of all sizes, lever forgings, stepped shafts and other types of products).
At your production and the production of your partners, we offer the implementation of automatic rolling lines (together with heating of blanks) of our own design and production. We also invite you to visit our company to familiarize you with the specified technology and equipment in detail. To justify the economic efficiency upon request, we are ready to prepare a technical and economic proposal in accordance with the drawings of parts planned for production provided by you.